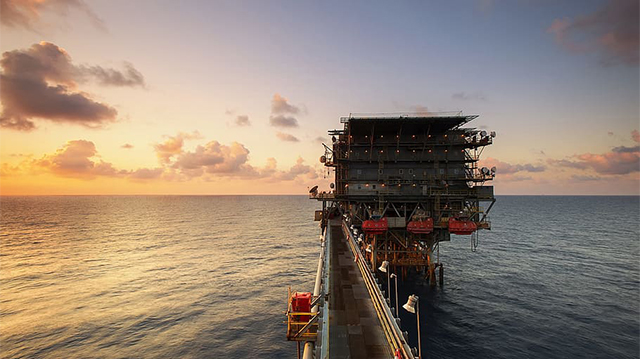
环保法规日趋严格成为中国油品清洁化及炼油过程清洁化技术进步的动力,也给企业炼油技术进步和生产管理带来更严峻挑战。
近年来,中国新投产、在建/规划的炼油项目体现了明显的基地化、大型化趋势。从燃料型向燃料-化工原料型转型是中国炼油行业可持续发展的大趋势,未来炼化一体化的深度和广度将发生重要变化。
炼油企业应按照“宜烯则烯、宜芳则芳、宜油则油”的原则,从分子角度最有效地利用原油资源,从化工角度优化炼油过程和产品线,从大量生产成品油转向生产高附加值油品和化工原料并重。利用新一代信息技术构建智能炼厂成为中国炼油行业未来重要的发展趋势。
炼油生产过程清洁环保,石油产品环境友好
环保法规日益严格,推动油品清洁化及炼油过程清洁化技术进步
近年来,中国密集出台了一系列行业监管与安全环保法律法规,对炼油工业的规范发展、能源消耗和污染物排放要求更严,监管也愈加严格,炼油企业面临的生态环境保护与安全生产压力不断加大。同时,社会对炼油企业的要求从过去重点关注生产过程的节能环保,进一步发展为生产环境友好型产品。环保法规日趋严格成为产品清洁化及炼油过程清洁化技术进步的动力,给企业炼油技术进步和生产管理带来更严峻挑战。
汽柴油质量标准升级加快,赶超国际先进标准
中国炼油工业在14年间完成了车用汽油、车用柴油从国Ⅱ到国Ⅵ的升级,实现了车用汽油超低硫、低烯烃、低芳烃、低苯的要求,柴油高十六烷值、超低硫、低芳烃的要求。过去10余年,汽油、柴油质量持续快速升级是中国炼油工业最重要的技术进步表现。目前,中国在汽、柴油产品标准方面的主要技术指标与欧美发达国家相当,实现了汽、柴油产品标准从过去多年跟跑向并跑的跨越。未来,中国清洁汽油的生产将继续在控制硫、芳烃、烯烃等有害杂质的同时,重点优化油品组成结构,增产高辛烷值汽油组分;柴油生产将继续保持超低硫、向深度脱芳方向发展,兼顾低凝柴油生产。
船用燃料油质量升级加快,船用燃料生产面临严峻挑战
在轻质油品质量标准快速升级的同时,重质油品船用燃料油质量升级也跟上步伐。国际海事组织(IMO)规定,自2020年1月起,在全球范围内船用燃料硫含量质量占比由现行的不超过3.5%降至不超过0.5%。中国作为国际海事组织成员国,提出珠三角、长三角、环渤海(京津冀)三个水域的船舶排放控制扩大到全国沿海12海里以及海南水域,要求船舶自2019年1月起在指定区域内使用硫含量在0.5%以下的燃油,在特定区域内使用硫含量在0.2%以下的燃油。船用燃料生产面临严峻挑战。
加快基础油质量升级,促进润滑油竞争力提升
中国是世界上最大的润滑油消费国,年消费量约为760万吨。内燃机油占润滑油总量的55%,中国内燃机油产品标准和评价方法长期跟随国外,整体落后2~3个质量级别。内燃机油中基础油约占80%~90%,提升基础油品质是其高性能化的关键。中国Ⅰ、Ⅱ类基础油产量占总产量的88%,缺乏高品质基础油生产关键技术,基础油结构失衡,高品质Ⅲ/Ⅳ类基础油的75%依赖进口。加快基础油质量升级、促进润滑油性能提升对国民经济发展具有重大影响。高含蜡石油基蜡油和F-T合成油富含长链烷烃,是生产Ⅲ/Ⅲ+类基础油的优质原料,但凝点高,其深度异构降凝是世界难题。由长链α-烯烃聚合加氢得到的规整结构异构烷烃-合成润滑油(PAO)具有超低温、超高黏度指数等优异性能,将得到快速发展。
炼油行业继续向规模化、大型化发展,产业集中度进一步提高
炼油生产规模经济特点显著,生产规模直接决定生产成本、资源利用率和市场竞争力。炼油生产降低成本的需求以及工程设计、设备制造和工程建设技术的进步推动炼油企业规模化和装置大型化。截至2018年底,中国1000万吨/年及以上规模级别的炼厂有28家,合计炼油能力3.7亿吨/年,占全国总炼油能力的44.5%;中国石油、中国石化的炼厂平均规模分别为765万吨/年和844万吨/年,已超过759万吨/年的世界平均水平。
近年来,中国新投产、在建/规划的炼油项目体现了明显的基地化、大型化趋势。这些项目的炼油能力都达到1000万吨/年以上的规模,采用世界先进的技术,其设计、建设、生产运行和管理都能达到世界先进水平。同时,民营企业成为中国炼油化工发展的生力军。
炼化一体化发展,提高应变竞争能力
一体化发展是炼化行业广泛采用、被实践证明富有成效的发展战略
一体化发展能节省投资,降低运营风险,提高资源的综合利用程度,增强应变能力和提高经济效益。目前,与炼化企业密切相关的一体化发展主要有三种形式或几种形式的复合:一是炼油和化工一体化发展;二是油田和炼化企业一体化(例如克拉玛依石化公司);三是炼化生产和热电或热电联产一体化(例如福建炼油化工有限公司)。其中炼油和化工一体化模式应用最多,宜油则油、宜化则化、油化结合,最大限度地有效利用石油资源,实现企业效益最佳化。
中国油品消费增速放缓
在中国的石油消费结构中,汽油、煤油、柴油合计占比为60%。柴油消费量基本达到峰值,2020年前将保持在1.75亿吨。汽油消费量在2025年左右达到峰值,可达1.7亿吨。航空煤油消费量将持续增长,2030年将达到6000万吨。当前,中国成品油消费增速放缓,消费柴汽比持续下降,预计2020年消费柴汽比降至约0.98,2030年将进一步下降至0.75。
中国化工原料需求旺盛
中国石化产品消费势头强劲,带动乙烯、丙烯、对二甲苯等主要基本有机原料需求旺盛。2018年中国乙烯产量约2372万吨,装置平均开工率保持在93%的高位,乙烯表观消费量为2630万吨,当量消费量(包括聚乙烯、乙二醇等衍生物消费乙烯)达到5010万吨,当量消费量的自给率不足50%。2018年中国丙烯产能达到3620万吨/年,产量约3005万吨,年均产能利用率达到83%,全年进口丙烯单体284万吨,丙烯表观消费量为3289万吨,当量消费量(包括聚丙烯、丙烯腈等衍生物消费丙烯)达到3869万吨,自给率达到77.7%。2018年中国对二甲苯(PX)产能为1379万吨/年,产量约1109万吨,产能利用率75%左右;受下游纺织业需求拉动,2018年中国对二甲苯进口量和表观消费量分别达到1590万吨和2699万吨,对二甲苯自给率仅有41%(见图5)[14][15]。在此背景下,炼厂多方式增产丙烯、芳烃及乙烯裂解原料,是炼化转型的有效途径。
炼厂从燃料型向燃料-化工原料型转型
从燃料型向燃料-化工原料型转型是中国炼油行业可持续发展的大趋势,未来炼化一体化的深度和广度将发生重要变化。从加工深度方面分析,催化裂化装置从生产汽、柴油燃料向采用深度催化裂化多产低碳烯烃方向发展;加氢裂化装置从以减压蜡油等为原料生产煤油、柴油中间馏分油向多产石脑油、航空煤油方向发展,具有原料适应性强、加工方案灵活、液体产品收率高、产品质量好等诸多优点,已成为现代炼厂由劣质、重质原料直接生产清洁油品及优质化工原料以及灵活调整柴汽比的重要生产技术;催化重整装置从多产汽油向多产芳烃方向发展。从原料加工的广度来看,加工原料除了重油、蜡油,已延伸到柴油加氢裂化、原油直接转化。
炼油企业应按照“宜烯则烯、宜芳则芳、宜油则油”的原则,从分子角度最有效地利用原油资源,从化工角度优化炼油过程和产品线,从大量生产成品油转向生产高附加值油品和化工原料并重,尤其是增产低碳烯烃、芳烃,从而进一步拓宽炼油行业发展空间。
埃克森美孚公司开发了原油直接制乙烯技术,开创了深度炼化一体化实践的先河。2014年,该公司在新加坡建成投运的产能为100万吨/年的原油直接生产乙烯装置,将原油直接供给裂解炉,在裂解炉的对流段和辐射段间各加入一台闪蒸罐,将原油预加热后通过闪蒸分离出较轻组分,并返回炉内的辐射段盘管进行裂解。闪蒸罐底部收集的重质液体组分被送至邻近的炼油厂或进入商业市场销售。与传统的石脑油裂解相比,该工艺每生产1吨乙烯可多获纯利润100~200美元。
智能化推动炼油行业高质量转型发展
为促进炼油行业提质增效、转型升级与内涵发展,利用新一代信息技术构建智能炼厂成为炼油行业一个重要的发展趋势。在“互联网+”为特征的新业态发展推动下,智能制造、智慧加油站、共享经济等新技术、新模式将推动传统炼化行业的改造,提升行业整体竞争能力。建立从原油采购、运输、炼化生产、仓储物流到销售等环节的智慧供应链和物流管理系统,对供应链各环节需求进行预测与供需平衡分析,实现全局优化,使整个供应链全面贯通以及供应链各环节高效协同。
建立生产计划优化、装置生产操作优化、运行过程效果评估、全流程实时仿真等智能生产运行体系,实现生产计划、调度、工艺流程、操作的优化控制,实现设备全生命周期管理和可预测性维护,优化全厂用能系统,提高生产系统管理效率,降低生产管理成本。
智能化还将推动分子炼油技术不断完善,实现对石油资源的最有效利用。“分子炼油”是通过分子识别技术(含油品分析和分子表征)、分子组成层次的模拟技术以及基于前两者的过程优化技术等,从分子水平上认识、加工和管理石油资源,实现对石油加工过程的极致精细化管理,推动石油组分实现“宜油则油、宜烯则烯、宜芳则芳”,使石油资源物尽其用。分子炼油概念将贯穿炼油企业计划、调度、生产操作等全流程。
在可以预见的未来,炼油工业作为世界上最大、最重要的加工业,在全球和中国仍将稳定成长。中国炼油工业的产能在不久的将来将超过10亿吨/年,居世界首位。中国石化、中国石油、民营企业、外资企业之间竞争将更加激烈,共同推动中国炼油工业的技术进步。中国炼油工业目前进入转型升级的关键时期,将通过清洁化、规模化、一体化、智能化等方式实现高质量发展。随着需求结构的变化,炼化一体化的深度和广度将发生重要变化,传统的炼油厂由过去主要生产燃料向生产原料、材料转变,未来还将出现新型的化工型炼油企业。